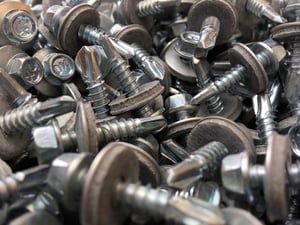
Case Study
Automated Packaging Case Study: Simultaneously Pack Three Different Bags of Nuts and Bolts
THE CLIENT/PRODUCT
Bags of Hardware; 8x10", 3x6"x 7½x7½"
THE CHALLENGE
Automate case packing and check weighing of three lines of bagged nuts and bolts that takes 15 people to accomplish.
The Solution
- 3 powered product infeed conveyors feed into Bombay-style case packers.
- A high-speed packing product conveyor separates product before feeding a counting funnel.
- The Bombay "door" is positioned below the counting funnel receiving product to full case count. The packer then receives a signal and drops product into the awaiting erected case which has been fed into the 3 case packers by a Combi 2-EZ® SB case erector.
- Once filled, the case count is verified by a Checkweigher and each case receives a print and applied label pre-programmed with product info relative to that line.
- Filled cases are indexed into a Combi TBS100FC top case sealer and sealed with adhesive tape. Rate of production is 12 cases per minute.
- Customer's productivity has increased 400%; staffing reduced (re-assigned) by 300%
Ready to put Combi's automated packaging equipment to work for you?
Fill out the form below or call us at 1.800.521.9072.
GET IN TOUCH WITH US
WANT TO FIND OUT WHAT COMBI CAN DO FOR YOU?
Need a Quote?
REQUEST A QUOTE
Stay Connected