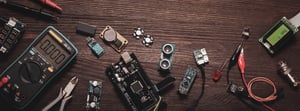
Case Study
Automated Packaging Case Study: Pack Irregular Shaped Electronic Parts
THE CLIENT/PRODUCT
Irregular Shaped Electronic Parts
THE CHALLENGE
Multiple pieces of fragile, irregularly shaped satellite components must be cradled with pulp end caps before being placed into RSC case. Also, product flyers must be manually placed into packed case before case sealing.
The Solution
- Fully customized Ergopack with two person pack station. The custom assembly line integrated case erector, check weigher and case sealer at 5 cpm
- Custom product fixtures designed and supplied that raise the product off conveyor, allowing clearance around the ends for placement of pulp caps
- Special indexing controls control product flow from both ends of the infeed conveyor
- Custom storage dispensers hold 180 pulp end caps. At the pack station, operator grabs a left and right handed cap, places them on product without having to touch the product, lifts product off fixture and places into waiting erected case.
- As filled cases advance to case sealer, any mispacked case is stopped at the check weigher.
THE RESULTS
Ready to put Combi's automated packaging equipment to work for you?
Fill out the form below or call us at 1.800.521.9072.
GET IN TOUCH WITH US
WANT TO FIND OUT WHAT COMBI CAN DO FOR YOU?
Need a Quote?
REQUEST A QUOTE
Stay Connected