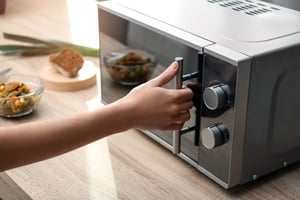
Case Study
Combi Provides Custom Equipment For A Flexible Product Line
THE CLIENT/PRODUCT
Ready Foods is a leader in the prepared foods industry. Known for its kettle-cooked soups, sauces and fillings, it provides kitchens across the country with delicious heat-and-serve menu items. With multiple locations and more than 250 employees, Ready Foods is a company on the move.
THE CHALLENGE
The soups and other products Ready Foods produce require flexible, pouch-style packaging. Since this type of packaging is prone to movement, it is very difficult, if not entirely impossible to carton pack using the traditional pick and place packaging machinery.
Ready Foods needed a solution that could keep up with its production output as well as be customized to its unique product line.
Additionally, automated packaging equipment represented a major departure from Ready Foods’ hand packaging process. The Ready Foods’ engineering team explored several packers before they were presented with the Combi solution.
According to Greg Hefter, Ready Foods’ Plant Engineer, these factors made it necessary to have a live equipment demonstration. He said, “The Combi team brought us out to a plant in Ohio that was running a very similar solution.”
“It was a big selling point for us to actually witness the difference Combi’s packer made.”
The Solution
- Combi Model DP/E2500 Drop Packer with Integrated Case Erector
- Combi Model TBS-100 FC Case Sealer
Ready Foods selected the Combi DP/E2500 Drop Packer for its ability to package flexible products by utilizing a “bomb bay ” door.
“To solve the problem of picking up our product, Combi thought outside of the box and suggested a pack and placer with a drop door,” said Hefter. “Essentially, it allows gravity to do the work by dropping the bags directly into the carton below.”
The installation was quick and kept Ready Foods right on schedule. And the support Combi provided prepared Ready Foods for an easy transition.
“We purchased the drop packer specifically to be installed in our new facility at the time,” said Hefter. “From the time we qualified the equipment until we started production was only a month or so.”
THE RESULTS
- Increased automation
- Reduced maintenance costs
It’s been 14 years since Ready Foods purchased its initial drop packer from Combi. In that time, it has been used to package millions of pounds of product every year. The original piece of equipment routinely runs three shifts per day, five days a week.
“We can count on it to keep up with production,” said Hefter. “The biggest way Combi helps keep us competitive is by reducing our downtime and maintenance costs.”
The long-term relationship Combi established with Ready Foods proved to be a very beneficial one.
“The Combi sales staff has really taken the time to understand our needs,” said Hefter. This in-depth knowledge enables Combi to make forward-thinking suggestions, tailored to Ready Foods’ business.
“The Combi packer has been so successful for us that we’ve actually come full circle—Combi now brings potential customers to see our solution in action.”